Trinity Leeds, Leeds
Developer: Land Securities plc
Architect: Chapman Taylor
Primary Contractor: Laing O'Rourke
Installer: Vetter UK
Design Consultants: Smart Crosby International
Design and Engineering:In partnership with Smart Crosby International Limited
In 2009, we were approached by leading architectural firm Chapman Taylor to provide GRC for the development of the £400 million iconic shopping centre, Trinity Leeds. The Architects were clear. They wanted a durable, aesthetically pleasing and cost effective surface for the inside of the development, which is why they turned to the UK’s leading supplier of glass reinforced concrete, GB Architectural Cladding Products.
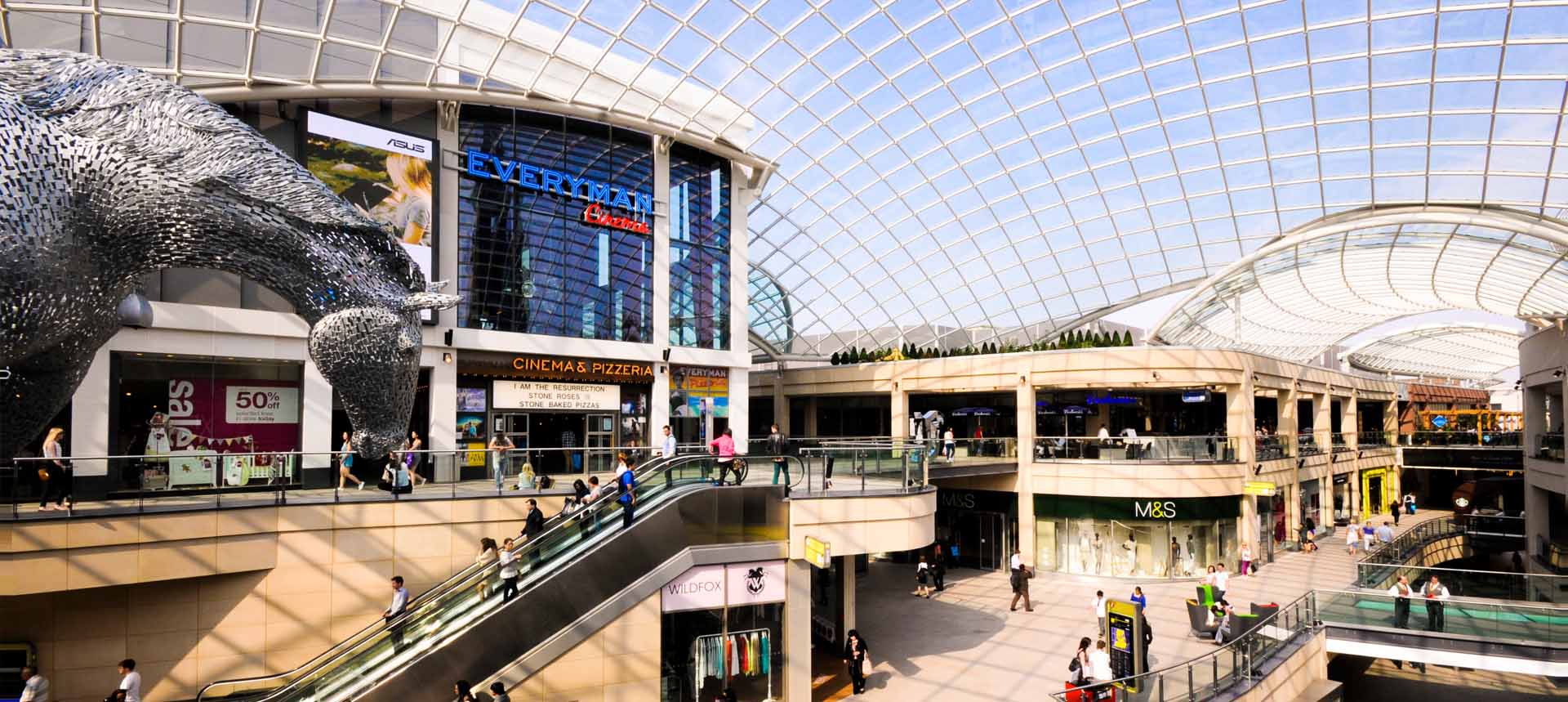
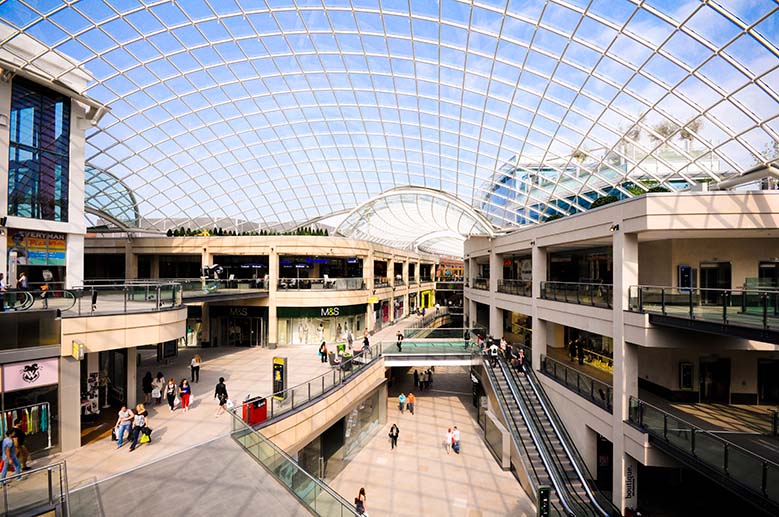
In 2009, we were approached by leading architectural firm Chapman Taylor to provide GRC for the development of the £400 million iconic shopping centre, Trinity Leeds. The Architects were clear. They wanted a durable, aesthetically pleasing and cost effective surface for the inside of the development, which is why they turned to the UK’s leading supplier of glass reinforced concrete, GB Architectural Cladding Products.
Having been officially appointed in 2011, GB Architectural Cladding Products collaborated with Chapman Taylor to design a GRC product which would meet their criteria and the high standards expected of a multi-million pound retail establishment. A product intended to look as good in 40+ years time as the day it was installed. In Autumn 2011, we commenced the manufacturing of a bespoke GRC product which not only met, but exceeded the expectations of all those involved with the design and installation process. In total, more than 4,000m2 of GRC was delivered and installed, with all shipments delivered on time and the project being delivered on budget; this being something which GB Architectural Cladding Products prides itself on, no matter the size or scale of the project at hand.
Our involvement came to an end in October 2012, just over six months before Leeds’ newest attraction opened to the general public. In its first year of opening, Trinity Leeds welcomed more than 22 million visitors through its doors, many of whom have admired the site’s architecture and appearance, with The Times complimenting the Trinity Centre’s ‘impressive, stylish interior’. In 2017, just four years after it opened, the site celebrated its 100,000,000th visitor.
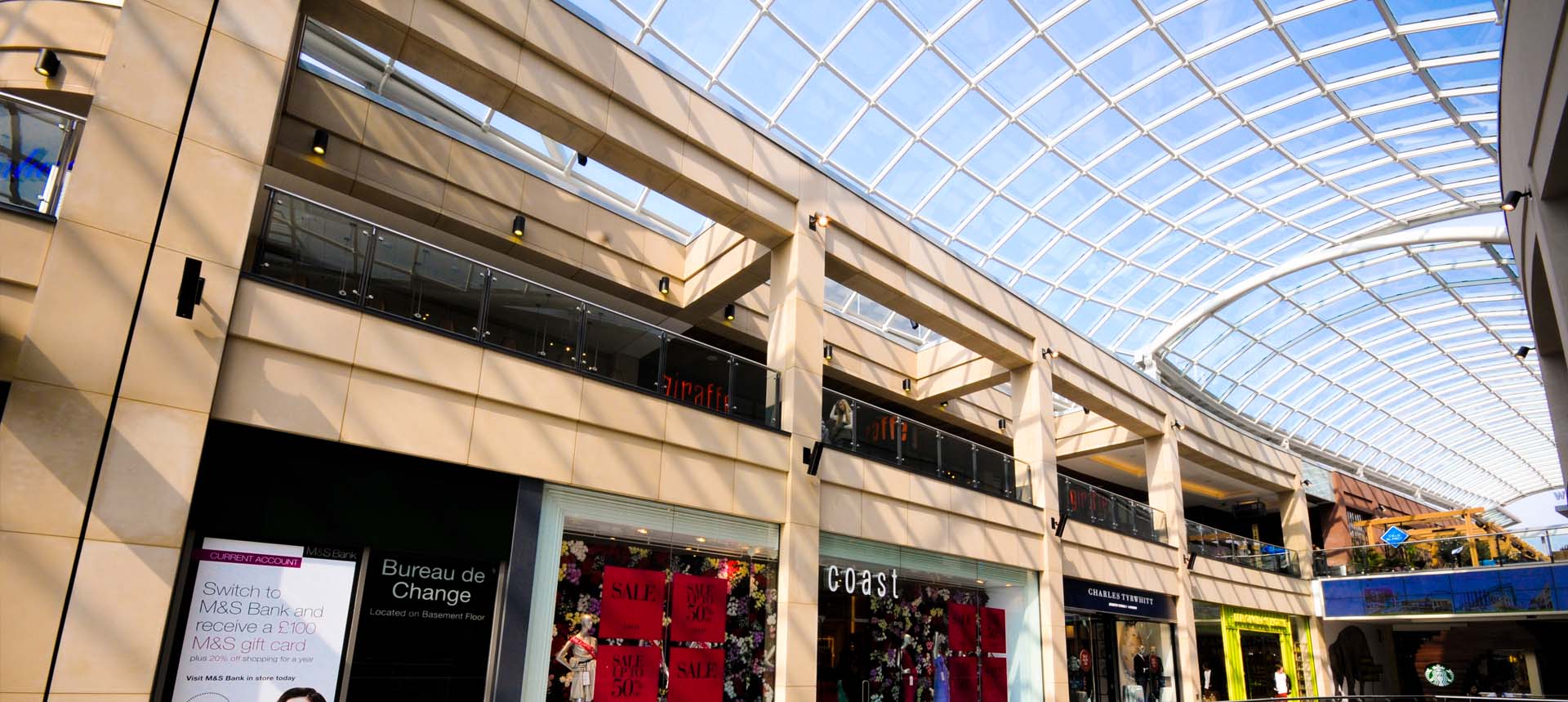
What the client says:
Robin Pinfield, Director, Chapman Taylor: “We are very pleased with the finished product.”
Matthew Wilkinson, Senior Project Manager, Laing O’Rourke: “This was a complex job – the sort an outside contractor, coming to it cold, might easily misjudge.”
What our Managing Director says:
“It was a very proud day for me when we were awarded the contract, not only because of the time and investment we had spent in trying to get it but it was the acknowledgement that we were trusted to deliver an impressive product to a strict schedule of time and cost.
“The project was a challenge because of the sheer number and complexity of the units involved, all of which had to be individually designed and created. “They then had to co-ordinate the fixings with the primary steelwork which was already in place. This fact constrained standard fixing details and so we had to design and manufacture panels for what was a uniquely technically demanding project.
“We have already seen new opportunities on the back of this project and I believe we are now firmly established as the best selection choice for architectural GRC cladding – clients are reassured with our experience and expertise. We have a proven track record of delivering high quality GRC products cost-effectively.”
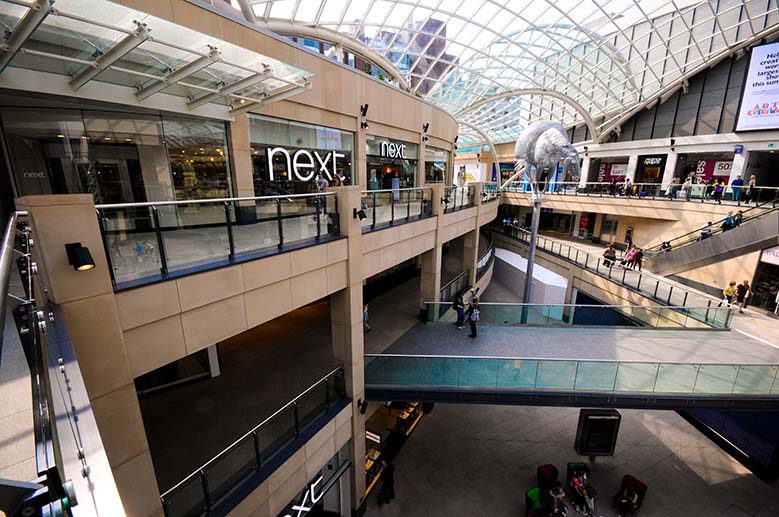